AFFRESCO PARTE 4 – LA PIETRA E IL FUOCO – ESTRAZIONE E COTTURA DELLA ROCCIA CALCAREA
Abbiamo finora allungato appena lo sguardo su quello che viene definito “il ciclo della calce”, cioè la vera e propria metamorfosi che compie la pietra, attraverso processi chimici, per trasformarsi in calce.
Cave e fornaci. La pietra e il fuoco. I primi elementi essenziali per la realizzazione della calce.
La cava per l’estrazione della pietra e la fornace per il fuoco.
Intanto bisogna precisare che rispetto alle cave di pietra da taglio, che devono fornire blocchi grandi, regolari e senza difetti, quelle per la pietra da calce, sono basate su procedimenti assai meno complessi. Le cave sono organizzate a gradoni, con un fronte e un piazzale, e per l’estrazione si cerca di sfruttare ogni difetto, ogni crepatura o fratturazione naturale. I massi possono essere distaccati dalla roccia madre con picconi e leve o con cunei infissi a martello nelle fessure e dopo il distacco le pietre vengono fatte rotolare sul piazzale, per essere ridotte in frammenti minori. Appena estratte hanno perciò forme irregolari; le dimensioni possono essere diverse, tuttavia non troppo piccole, né troppo grandi, in modo da agevolare le operazioni di trasporto: la lunghezza ideale non deve superare i 20-30 centimetri.
A questo punto ha inizio l’operazione vera e propria di trasformazione della roccia calcarea estratta.
Il primo passaggio consiste nella calcinazione o cottura della pietra che si compie appunto nella fornace. I metodi di cottura più semplici, conosciuti fin dai tempi più antichi, erano basati sull’utilizzo di cavità nel terreno, generalmente di forma circolare e circondate da uno spesso muro a secco nelle quali si disponeva il combustibile per cuocere la pietra in cumuli. L’operazione di carico era sicuramente una delle più delicate specialmente nella sua primissima fase. Si cominciava a riempire la fornace lasciando alla base un vano a forma di volta per poter accendere il fuoco. In seguito la si riempiva fino all’orlo con dei pezzi di calcare mettendo le pietre più grosse al centro, dove il calore era più elevato, e quelle più piccole ai bordi lasciando degli interstizi che permettessero alla fiamma un facile accesso alla massa soprastante. Il cumulo veniva poi coperto con argilla per impedire il disperdersi del calore. La fase di calcinazione durava circa una settimana.
Inizialmente si preriscaldava lentamente l’intera massa accendendo un fuoco soffocato sotto la volta per una durata di circa dodici ore. Questa procedura era indispensabile in quanto una fiammata troppo violenta avrebbe causato una tale espansione dei vapori che si sviluppano durante la calcinazione da ridurre in pezzi la volta del forno. In seguito si aumentava gradualmente la temperatura fino a far diventare le pietre di un bel rosso intenso. A partire da questo momento il fuoco doveva essere mantenuto costante. Se una corrente d’aria fredda avesse raggiunto la massa rovente i sassi si sarebbero anneriti e la qualità del prodotto finale ne avrebbe sicuramente risentito. Quando si notava un sesto dell’abbassamento della massa iniziale (dovuto alla perdita dell’acido carbonico, cento parti di calcarea contengono circa 43 parti di gas acido carbonico) e la fiamma usciva senza emettere fumo, e questo circa 4 o 5 giorni dopo, la calcinazione era giunta al termine.
In pratica la cottura, mantenuta a una temperatura tra gli 800 e i 1000 °C dà luogo a una reazione chimica per cui il calcare CaCO3, assorbendo calore, libera anidride carbonica CO2 e si trasforma in ossido di calcio CaO, comunemente chiamato calce viva.
Questo tipo di forno era detto a fuoco alternato perché per passare da una fornaciata all’altra era indispensabile spegnere il fuoco che la alimentava onde permettere le operazioni di carico e scarico.
Come anche quelli più moderni che li seguirono venivano costruiti nelle immediate vicinanze della cava per ridurre al minimo le operazioni di traporto del sasso che perde parte del suo peso soltanto dopo la calcinazione.
Attorno alla fornace ruotava la vita del calcinarolo o calcinaro o fornaciaro che doveva sorvegliare costantemente il fuoco durante la cottura della pietra calcarea. I calcinari non avevano certo le conoscenze scientifiche per capire la trasformazione fisico-chimica che subiva la pietra calcarea sottoposta a cottura alla temperatura prossima ai mille gradi centigradi; tuttavia l’esperienza tramandata per generazioni aveva portato la loro tecnica nella produzione della calce ad un livello tale per cui nulla era lasciato al caso. A cominciare dalle cave dove veniva estratta la materia prima e dove venivano scelti gli strati più puri della pietra; al loro dimensionamento più adatto per caricare la fornace; alla maestria con cui questo caricamento veniva eseguito; allo scarto del materiale mal cotto. Tutto contribuiva ad offrire sul mercato un prodotto di ottima qualità. Era una vita comunque molto dura. La fornace doveva essere sorvegliata giorno e notte. Tra l’altro l’attività lavorativa iniziava in periodi ben distinti: in primavera ed in autunno. La scelta del tempo escludeva i periodi critici dell’estate e dell’inverno. Il primo per evitare l’eccessiva calura in prossimità della fornace accesa. Il secondo per evitare la stagione piovosa. Una pioggia od un acquazzone ad inizio cottura non comportava seri danni, ma se questa cadeva nella fase terminale della cottura stessa, reagendo con l’ossido di calcio ormai formato, sfarinava la pietra causando la perdita di buona parte del prodotto. I calcinari avevano anche un secondo lavoro, quasi sempre legato all’agricoltura, che permetteva di lavorare anche nei tempi morti.
A tal proposito ne parla anche Vincenzo Scamozzi:
“ ……Le calcine ordinariamente si fanno il mese di Marzo e Aprile, essendo che allora s’incomincia gagliardamente a fabricare e gli huomini e i bestiami sono liberi da gli affari delle campagne; si come altre se ne fanno dopo alle vendemmie…….
…Ad ogni calcara fa bisogno almeno due persone, che vicindeuolmente attendino al foco, il quale
si dà prima in bocca di legne sottili e secche: e poi all’indentro di legne mezane, che faccino buona fiamma; perché le molto forti, e grosse abbrucciano la calce, e anco bisogno di tratto in tratto sollevar le legne; acciò vi entri l’aria sotto….
….A’ principio il foco fa il fumo denso e scuro, e perciò le pietre vengono nere da esso e dal caligine, e poi s’infocano come braccia e a poco a poco il fumo si va schiarado che è segno che sia leuato l’humidità e le pietre per ordinario si cuoceno in 4 e al più 5 giorni e notti continue di foco il quale sta 3 e 4 giorni à comparire nel disopra alla calcara …..
…..I segni che le pietre nella fornace siano cotte e diuenute calce sono principalmente questi, che il fuoco russa, perché non hà materia da consumare e diuenghi di colore azurro vicino alle pietre e non faccia fumo, ma eschi il calor chiaro come l’Aria, e tutta la massa delle pietre cala alquanto a basso; perché le pietre diuengono minori e assai più leggieri e di peso, i due terzi (come dice anche Vitruvio) ouero tre quinti di prima e si sentono di un suono più dolce e grato e hanno perso del tutto l’odore e colore della pietra e acquistato quello della calce e più bianchezza”
e continua così in modo molto approfondito e con tanti altri piccoli accorgimenti nel suo scritto “L’Idea dell’Architettura Universale” di Vincenzo Scamozzi 1615 – Libro VII – cap. XVIII, pag. 227/228.
La poesia che si respira nella descrizione dell’operazione di calcinazione che ci ha lasciato il famoso architetto è un’esperienza unica. Non si parla di procedimenti chimici, di dati scientifici, di gradi o misure; la descrizione si basa sull’osservazione dell’esperienza diretta, sistema di grande efficacia per gli operatori del settore che a quei tempi probabilmente non sapevano né leggere né scrivere. Lo Scamozzi cita anche l’architetto e ingegnere dell’antica Roma Marco Vitruvio Pollione che nella sua pubblicazione “De Architectura” del 13 a.C. fornisce una serie di informazioni dettagliate riguardo le modalità di costruzione (nel capitolo V discorre della calce).
Certo una fornace di questo tipo poteva sopperire al fabbisogno di piccole comunità e spesso le calchere venivano costruite nei pressi di grandi edifici, grandi opere in costruzione. A conferma di questo nel 2008-2009 una campagna di scavi condotta a Châtel-Argent di Villeneuve in Valle d’Aosta ha portato alla luce un forno da calce facente parte del grande cantiere edile che venne impiantato sul sito del castello tra il 1274 e il 1275 con lo scopo di provvedere ad una vera e propria ricostruzione della fortificazione ormai ammalorata.
La posizione del forno, nel punto più alto del sito fortificato e contro una parete rocciosa in pendenza da sud verso nord, risponde sia alla necessità di predisporre il cantiere nelle vicinanze del luogo prescelto per la costruzione della torre cilindrica, sia alla regola empirica che prevedeva di interrare la fornace per almeno la metà della sua altezza per aumentarne il grado di coibentazione, essenziale per la fase di cottura in strutture che, con tecnologie ancora prescientifiche, dovevano raggiungere e conservare per parecchi giorni temperature vicine ai 900° C.
Ma negli anni a seguire e, nel nostro territorio precisamente a partire dalla seconda metà dell’ottocento, l’esigenza di una produzione più industriale impose la tecnologia costruttiva delle nuove “fornaci a fuoco continuo”. L’invenzione di questi forni fu dovuta all’ingegnere berlinese Friedrich Eduard Hoffmann, ed è databile alla metà del Diciannovesimo secolo, 1858, in piena Rivoluzione Industriale. La concessione del brevetto Hoffmann in Italia risale invece al 1864.
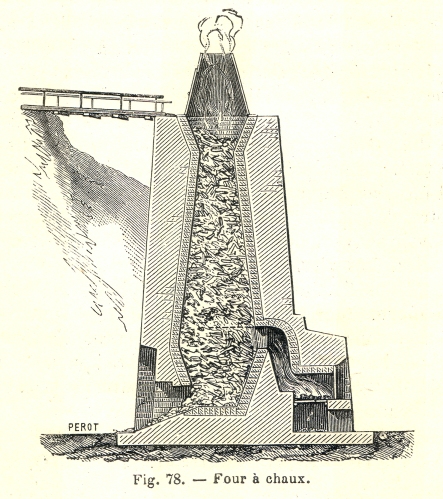
Fornace a fuoco continuo – Schema tratto da ”Leçons élémentaires de chimie (B.Bussard, H.Dubois).” 1906
Si tratta di torri alte fino a più di 15 metri costruite con robusti mattoni in pietrame e calce il cui spessore si riduce dal basso verso l’alto e sono quelle riconoscibili anche a Ispra e Caldè sulla sponda lombarda del Lago Maggiore, anche se queste sono di dimensioni minori. Le forme esterne sono variabili, a tronco di cono, o a imbuto con fumaiolo più o meno alto. Venivano costruite vicino a un terreno scosceso per poter raggiungere il piano di cava con la parte superiore della costruzione dove era presente l’apertura che serviva per il caricamento della pietra. A tal scopo ci si serviva anche di ponticelli dove scorrevano i carrelli colmi di pietre sminuzzate. Le pareti esterne poi erano separate dal forno da intercapedini riempite di sabbia o di cenere per impedire la dispersione del calore. All’esterno erano cerchiate con fasciature perimetrali in ferro per preservare dalle deformazioni conseguenti al calore. Ad una certa altezza venivano praticati dei fori che servivano a far circolare l’aria. L’innovazione strutturale riguardava la posizione dei forni per la cottura, da uno a due, che erano laterali e posti a qualche metro dal suolo, più in alto dell’apertura di scarico. Non era più necessario quindi spegnere il fuoco per scaricare la pietra cotta. Il combustibile usato era costituito da carbon fossile. A questa operazione era addetto il fuochista che osservava dei turni di lavori di otto ore al termine del quale provvedeva anche all’estrazione della calce prodotta nel suo turno.
La calce così spenta, detta anche calce viva dal crepitio che le pietre emettono dopo la cottura tanto da sembrar materia viva, deve essere riposta in luoghi asciutti ed areati. Questo per evitare che si inneschi prematuramente il passaggio successivo di “spegnimento”, di cui vedremo nel prossimo capitolo, operazione fondamentale per la realizzazione del grassello utilizzabile in edilizia e soprattutto per realizzare affreschi, nostro indiscusso obbiettivo finale.
Necessario ribadire ancora che dopo la seconda guerra mondiale l’industria, per la necessità di una produzione in grandi quantità in tempi brevi, ha mano a mano eliminato questo tipo di forno sostituendoli con i più economici forni a olio combustibile o a metano. Il prodotto finale però non ha più le stesse caratteristiche organolettriche, di struttura cristallina, di purezza e di biancore.
Curiosità: l’ossido di calcio (o calce viva) si presenta come un solido incolore e inodore. È un composto irritante e ha caratteristiche prettamente basiche. L’ossido di calcio miscelato con l’acqua genera una reazione esotermica secondo questa reazione CaO + H O ↔ Ca(OH) + 1136 Kj/Kg di CaO Questa reazione viene utilizzata spesso per produrre bevande in lattina calde L’ossido di calcio viene inserito nel fondo della lattina, la pressione di una membrana sul fondo miscela l’ossido di calcio con l’acqua e la reazione esotermica scalda la bevanda.
Paola Mangano
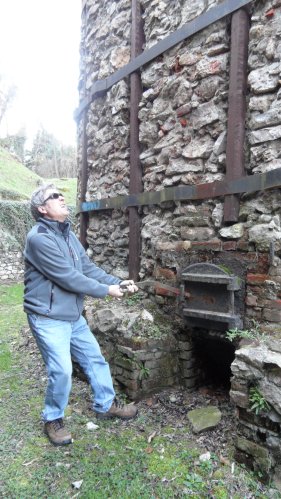
Mauro Nicora alle prese con uno dei forni della Fornace Binda di Ispra – Come fornaciaro non lo vedo adatto
Nessun commento:
Posta un commento